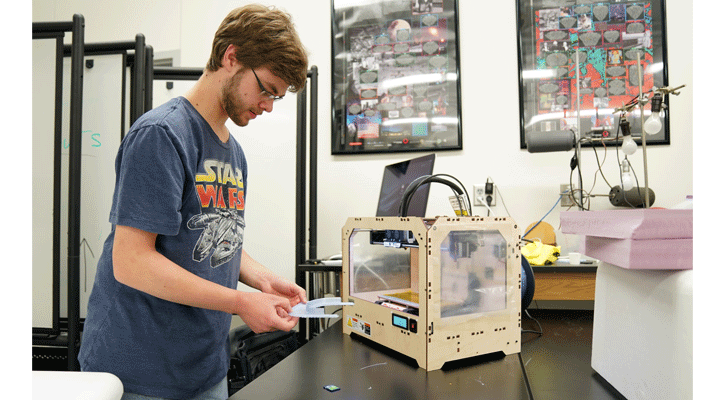
By Heather Johnson
NORTH PLATTE, Neb.-A North Platte Community College student is making face shields to help protect local health care providers against COVID-19.
Packer Daily is a member of NPCC’s STEM Club and is also a nutrition services employee at Great Plains Health. For the past couple of weeks, he has been creating face shields using a MakerBot 3-D printer that belongs to the college’s engineering department.
“Great Plains Health sent out a general request for personal protective equipment, and face shields were some of the things it was in need of,” Daily said. “My dad [NPCC physics and engineering instructor Jared Daily] asked me if I would be interested in making some. I was familiar with the printer and am already on the hospital’s payroll, so it just made sense.”
Packer began the endeavor April 8 – churning out five masks.
“It takes about 100 minutes to print each one,” Packer said. “Once the MakerBot gets started, I can stay in the general area and work on other things. Lately, I’ve been able to do my homework while also monitoring the printing process.”
He has enough materials to make several hundred face shields. Packer uses the printer to create plastic visors then attaches transparent plastic sheets for the shields. They are the same kind of computer printable sheets used for overhead projectors. The visors fasten to a person’s head with elastic or Velcro straps.
“MakerBot actually had a pattern for the face shields on its website,” Packer said. “Each one measures about 8.5 by 11 inches from top to bottom.”
The project has taught him valuable skills in a field he plans to pursue as a career.
“I want to stay pretty close to this kind of work for the rest of my life,” Packer said. “I would eventually like to be a physicist in a lab or at a college. This project has been a good lesson in prototyping – which is the process of creating an idea for mass producing a product. That’s basically the field that 3-D printers were invented for.”
The project has taken keen observation skills and has pushed Packer to think outside the box in terms of efficiency and productivity.
“I’ve been able to come up with better ideas for designing and printing the shields,” Packer said. “People have a tendency to expect a print job to be perfect every time, but unlike a normal printer, 3-D printers force users to think about the structural integrity of a design – what makes a design more stable and likely to succeed as many times as possible.”
Improving systems, especially those he has created, and finding simpler ways of doing things are some of his favorite challenges.
“It’s also just a good feeling to be an ordinary person having an effect in a time of need,” Packer said. “The hospital is always encouraging its employees to give back and help out wherever they can. This is my way of doing that.”
Packer has been taking the face shields to Great Plains Health as he gets them done.